- Homepage
- News and Features
- Loch Lomond: Stopping the sink at the UK's wettest golf club
Loch Lomond: Stopping the sink at the UK's wettest golf club
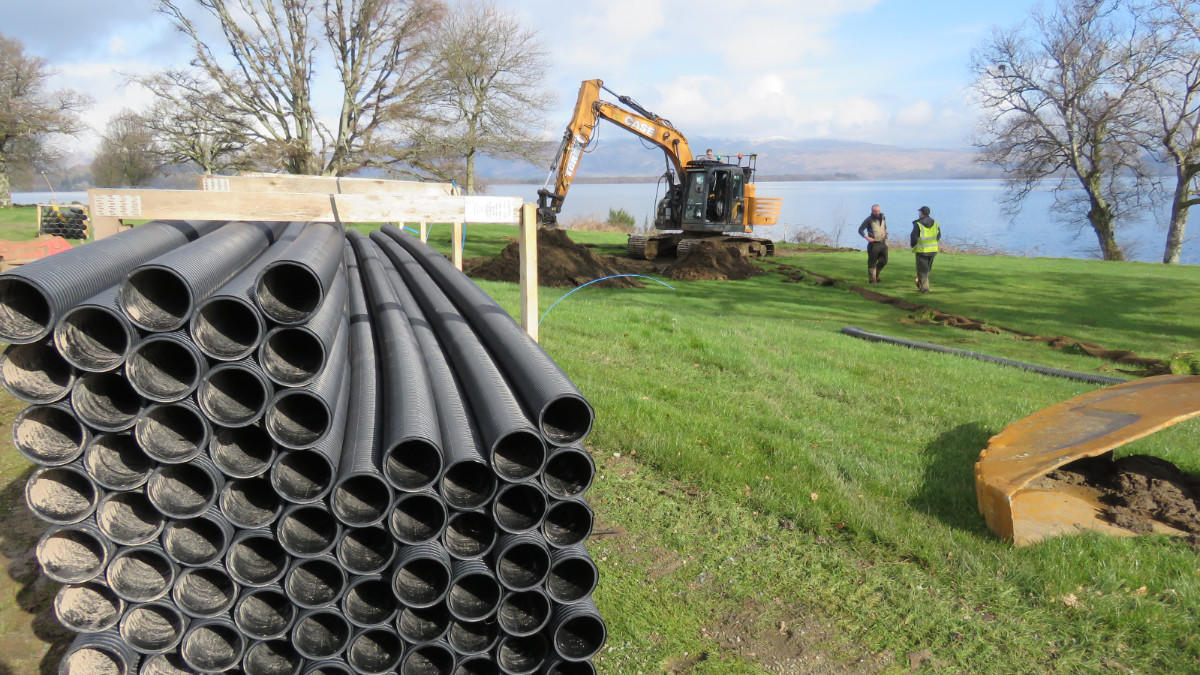
Almost 2 metres of annual rainfall and a soil infiltration rate of 0.01mm per hour does not make for fine turf conditions.
If anyone asks David Cole MG to justify the sheer enormity of the project that’s taking place at Loch Lomond Golf Club, those are the sort of statistics he quotes.
The renovation of Loch Lomond has been described as the largest construction project on an existing golf course in the history of the British golf industry. At Continue to Learn 2021 David gave an in‑depth look at the work that has taken place at the former host of the Scottish Open, and this feature gives an introduction to some of the work that has taken place and the challenges it has placed on those attempting to complete the work.
The original construction of Loch Lomond Golf Club on the banks of the United Kingdom’s largest lake makes for pretty cringeworthy reading when viewed through a modern lens. When you hear of some of the materials that contractors utilised to transform a peat bog into a golf course, it is no surprise that overcoming drainage issues has been a mainstay of the greenkeeping team’s responsibilities ever since.
Driving around the unaltered areas of the course, buggy tyres squelched loudly and you certainly wouldn’t wear your best golf shoes to play the course.
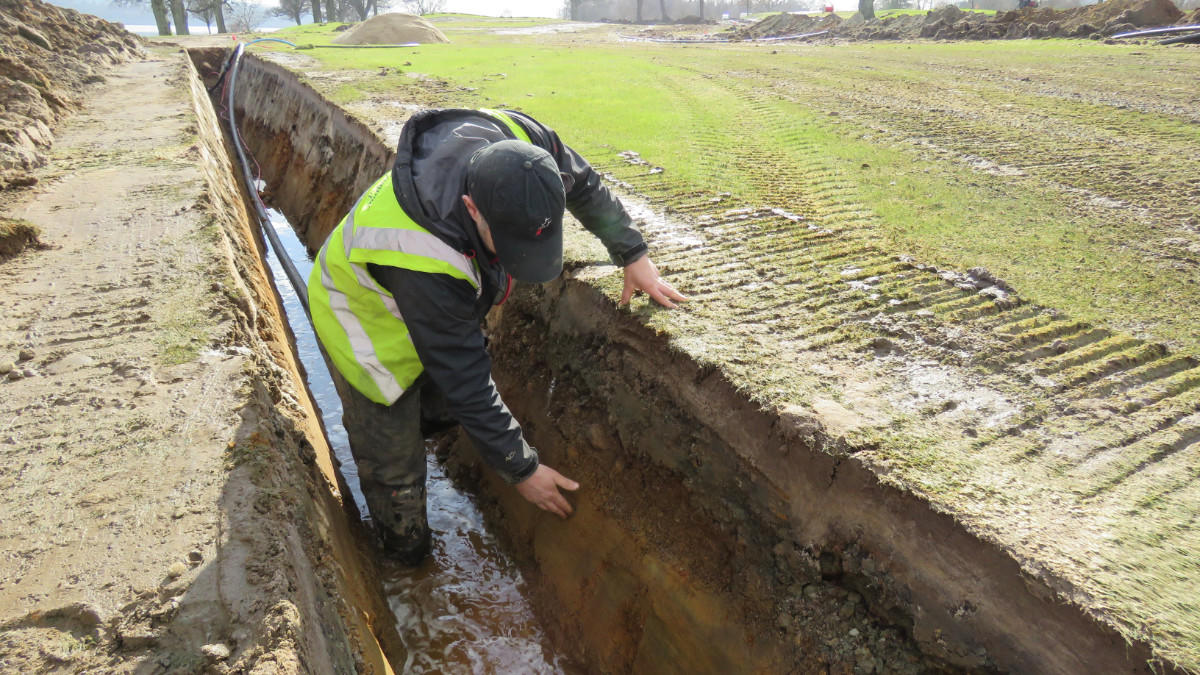
There is a famous story that course architect Tom Weiskopf sank up to his waist in a bog on the site of the 14th hole during the original construction. It was a terrifying ordeal made all the worse by the memory of a bulldozer that had been entirely swallowed up by the peat bog earlier in the construction, vanishing without a trace. Faced by the very real prospect of sinking deeper into the bog, Weiskopf spent up to four hours pulling himself to safety and wouldn’t speak about what happened for years afterwards.
The locals, and that includes course manager David, know the land is not to be taken lightly and that there are consequences of locating a course in the wettest region of the UK. Drainage has always been paramount and related installation has been ongoing since the club opened in 1994.
In 2015, after another wet season, David realised the course and the drainage infrastructure required a serious overhaul. The intense drainage network that was installed in the early 2000s was in decline from silt and sediment ingress into the pipes, slowing down the high rainfall removal. The ongoing drainage work and cultural practices were not comprehensive enough to deal with the high rainfall volumes in combination » with the impervious soils.
David explained: “The site is always vulnerable to saturated conditions, but from that year on we really witnessed the decline in drainage performance. At times we could not mow the fairways for weeks on end. If we got a short dry spell, we would try to cram in all the mowing and other work that we could, because we knew it would soon rain and the course would become very wet quickly again.”
Loch Lomond’s greens, 30% of the tees and some approaches are constructed of a sand‑based rootzone. These surfaces drain rapidly and are what kept the course playable. These also helped the team demonstrate how, with serious investment, the whole course could be well‑presented, despite the climatic situation.
David added: “Mentally it was very draining (pardon the pun) for the entire team and coming into work every day was frustrating and very stressful. As a course manager and greenkeeper, all you want to do is present good golf course conditions that your members and their guests deserve. But the many external elements that were out of our control were making the job so much harder. Even on any days off it was difficult to concentrate because all you were thinking about was rainfall and how we were going to deal with it for the next day or week.”
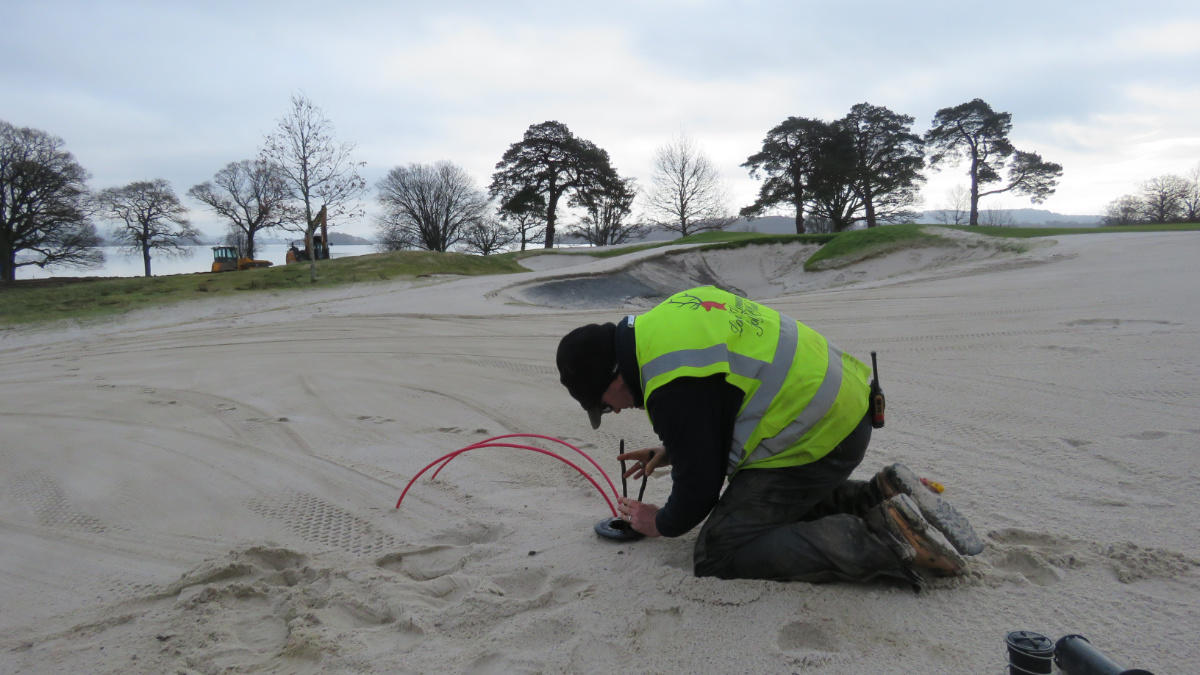
The team was trying to come up with affordable solutions and fixes, but even simple aeration and sand topdressing operations were problematic due to the weather and ground conditions by not being able to get equipment onto the turf.
Situated at the gateway to the Scottish Highlands, that rainfall comes on average 222 days a year. Weather fronts move in off the Atlantic Ocean and get stuck on the high mountains. The higher the peaks the more rainfall will fall.
When it was constructed in the late 1980s to early 1990s, Tom Weiskopf and the team were faced with the challenge of building a large portion of the golf course on top of peat bogs. Allegedly, around 1million cubic metres of made‑up ground was mobilised onto to the site to build the course and stabilise on top of the peat bog. The material came from the construction of the A82 road, a demolished World War 2 torpedo factory and some borrow pits on site.
David added: “This combination of spoil didn’t form a great growing medium. It is a mixture of rock and rubble and to top it all off they put a layer of what they thought was topsoil but was just clay on top. The turf just sits on top and because of the rainfall we get here it survives, but there’s no real rooting structure to it whatsoever. This makes it difficult to manage and deterioration is quick.”
A hydraulic connectivity test conducted by the STRI in 2016 discovered that the inherited soil profile infiltration rates on the site were as low as 0.01mm an hour on a site that receives 2,000mm of rain a year. Fine silt was seeping into the drainage pipes and they were running at around 20% efficiency – and in some cases worse. As there are miles and miles of drainage pipes across each hole, it is very difficult to diagnose the cause of any problems that occurred. Without extensive exploration, we didn’t know if there was one main pipe blocked or all the pipes. The vast playing surfaces of the fairways and rough – around 35 hectares – is expensive to manage, and with small conducive weather windows it is difficult to make any small improvements.
“I was getting really concerned that these areas were not small and localised anymore, but they covered thousands of metres,” said David. “It was so disappointing to see the decline in turf conditions as investment and tireless hours of work was supported by the owners and carried out by so many greens crews over a long period of time. As the drainage declined, the decline in turf conditions was even more rapid.”
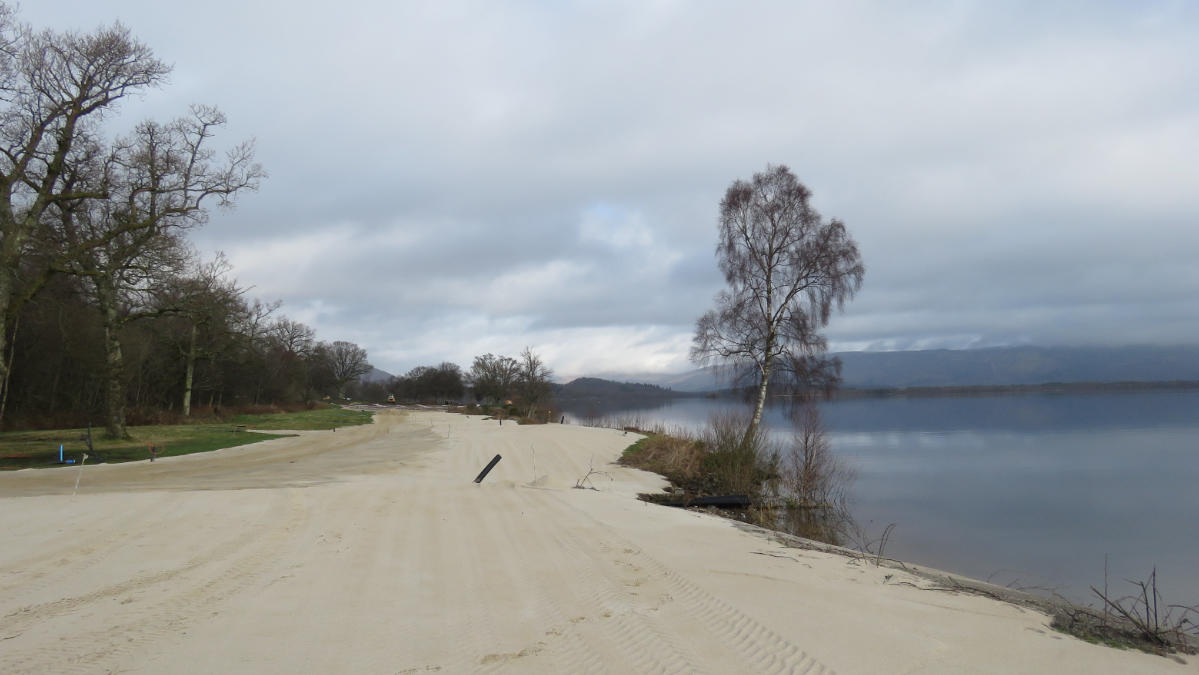
It had become clear to David that if the golf course were to remain playable and not lose its reputation as one of the finest clubs in golf, a large‑scale drainage project needed to take place. But with the 400‑year‑old Rossdhu House at its centre and another 45 rooms in various lodges across the estate all requiring a share of the annual capital expenditure budget, a long‑term finance strategy was required, knowing that the project would cost millions of pounds to complete.
"We retained a few agronomy consultants to challenge, support and consider various options to address the drainage flaws,” said David. “But the soil profile was also half of the problem. If we only addressed the drainage network, then we would have similar problems of silt ingress into pipes in the future and poor turf conditions in‑between drain lines with our climatic conditions. It’s hard to put into words just how poor the soil structure is.”
Each of the consultants supported the drainage upgrade and the vital sand cap. The existing sand‑capped sections of tees, approaches and greens demonstrated success and helped management and owners have confidence in the proposed renovation and investment. However, with a new sand cap, the irrigation system required fully upgrading to ensure adequate water coverage in drier spells and for the grow‑in periods.
An existing and ongoing project at the club was the renovation of tees and bunkers and so the areas still to be upgraded were included into the full renovation budget. This meant the original cost to drain and sand cap increased dramatically, and all had to be justified .
David calculated that the entire project would need to include:
- A new irrigation system that encompassed greens, surrounds, tees, fairways, and some roughs
- A rebuild of tees not already renovated, making them larger and more rectilinear and adding new forward tees
- A rebuild of bunkers not already renovated including minor contour changes, new drainage, new erosion liner and new sand
- A rebuild of fairways with minor contour changes
- An upgrade and future‑proofing of drainage network to all surfaces
- A 200‑225mm deep sand cap across all renovated surfaces
- Re‑grassing to all surfaces, using approximately 75% turf and 25% seed.
In 2017, after a period of campaigning, meetings and demonstrating through the success of smaller works what could be achieved, and from support of the management and board of directors, the club made the decision to approve the project and commence with work in the winter of 2017.
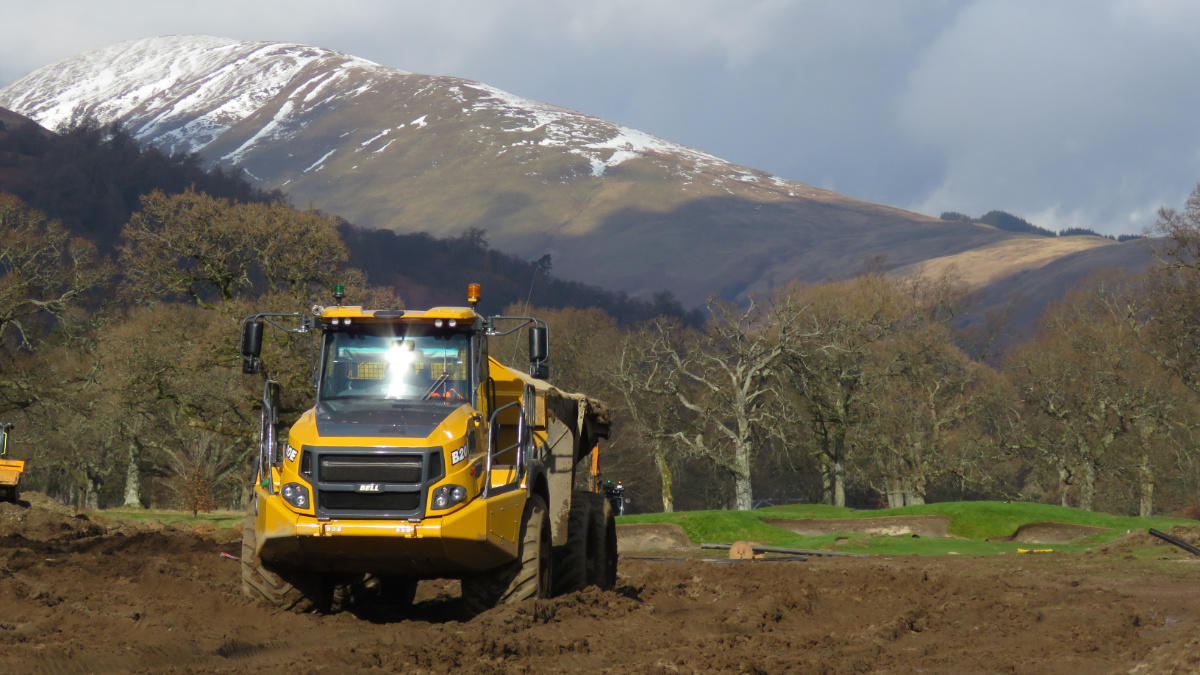
Due to the club’s international membership – there are 600 members from 35 different countries – the renovation works had to be carried out in the off seasons, so as not to disturb the member experience and the club’s most profitable part of the year. This meant that after each phase of works, 18 holes had to be ready for play on 1 April each year.
David said: “We totally understood the decision to carry out the renovation through the winter periods. It was always going to be difficult to close the course or certain holes during the season and not affect the experience of members, which would then potentially affect revenue streams within the business. We employ around 150 full time and 100 seasonal staff and we could not risk disturbing the main golfing season, which in turn could affect employee numbers. However, we knew from experience that doing this vast project and excavation » work in the off season, when 1 metre of rain will fall and with the threat of flooding, snow and ice, we knew it was going to be one heck of a challenge, both mentally and physically.
The principal contractor was Esie O’ Mahoney, working first with Sol Golf in 2017‑18 and then from 2018 with his new GolfLink company. Adrian Mortram was brought in to design the irrigation and the Toro Lynx system was used, with Aquaturf Solutions brought in as the installer. David praised all the contractors and gave a special mention to his overall team for all their efforts, especially the ones heavily involved in the project and grow in. He added: “They all worked for long hours throughout the winter in horrible, brutal conditions and yet they have produced the goods. They are all completely invested and understand what needs to be done, so I cannot thank and praise them enough.”
In the first year the team completed two holes and the plan was for four to six holes to be completed each year thereafter. In the winter of 2018‑19 the team managed to complete eight holes and another six in 2019‑20, before COVID‑19 halted progress. This winter the final two holes are under construction and will be ready for opening in March 2021. The course has opened as planned on 1 April each year, apart from one hole in 2019 that opened mid‑April.
The Loch Lomond project is an incredible case study about the challenges of maintaining a golf course in difficult environmental conditions, the need for continuous and sustained investment in your course and the need for effective communication at every level of the club if you are to achieve your ambitions.
This feature has only scratched the surface and David Cole spoke at Continue to Learn 2021 in greater depth about the project. BIGGA members will soon be able to access this content in the Members' Area of the BIGGA website.
Author

Karl Hansell
Karl has been head of communications for BIGGA since March 2016. His duties include editing the monthly Greenkeeper International magazine, in addition to other communications activities for the association.